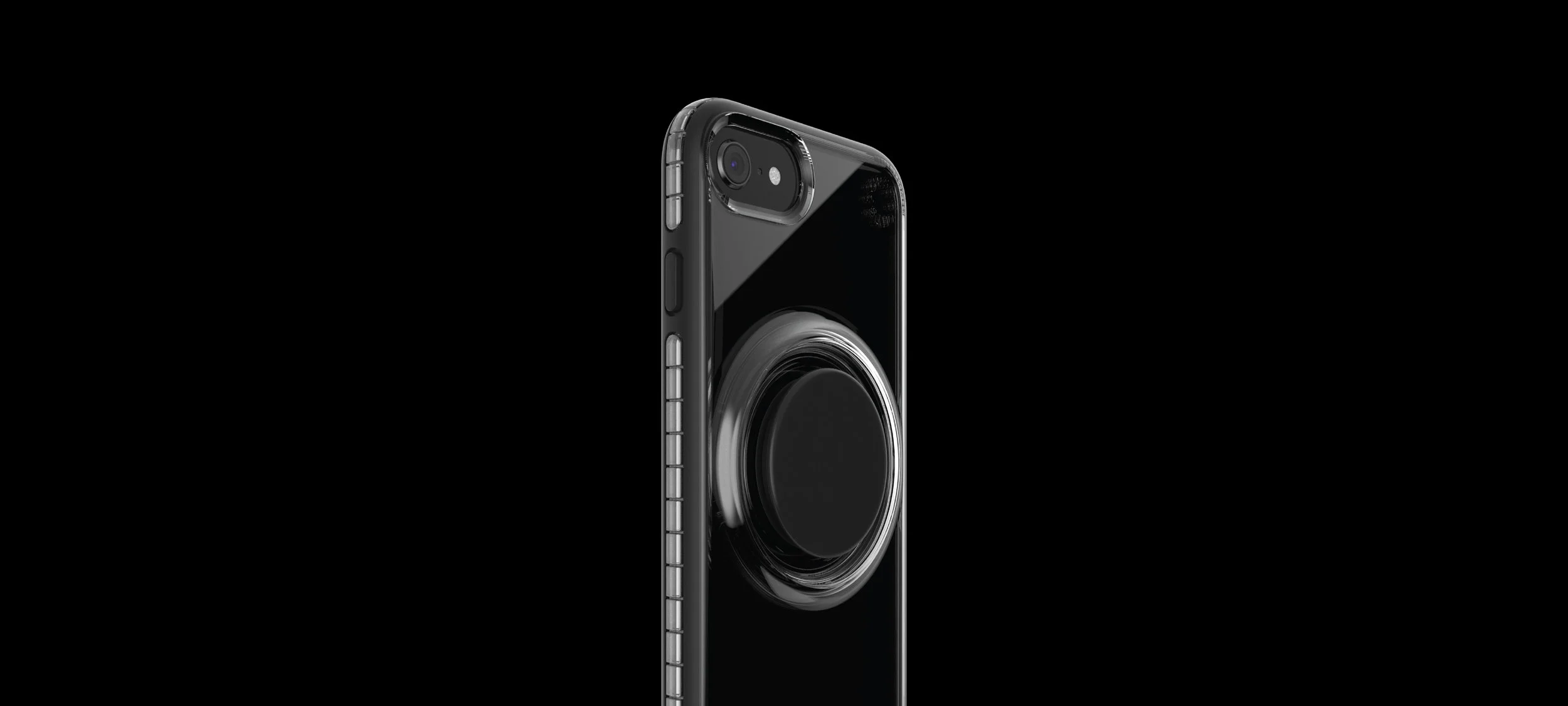
PopCase AIR
for iPhone
ROLE Lead Industrial Designer, PopSockets
1 iPhone 2 Blow-molded airbags 3 TPU bumper 4 TPU "accordion" 5 PC back 6 PC "platform" 7 PopSocket
PROBLEM
Dozens of brands are flooding the phone case market with the exact same products.
How can PopSockets offer a superior, differentiated product?
1
Unique protection
2
Enhanced functionality
1
Unique protection
INSPIRATION I looked towards the advancements that the shoe industry is making with blow-molded shoe soles for a protection story that has never been told in the case space. Pockets of air = ultimate cushion against bumps and drops.
MATERIAL RESEARCH I was dealing with a completely new process and material that I had never worked with before. I gathered various air-filled products to begin understanding the capabilities and limitations of the blow-molding process.
SKETCHING + IDEATION I began exploring different architectures for a blow-molded case. I sketched through various cross-sections to determine the appropriate stack-up of materials; a soft TPU inner layer with a hard PC exterior shell was the market norm for protection.. how could I re-imagine what this needed to be, and where would the air pockets come into play?
VENDOR FEEDBACK Developing a close relationship with a blow-molding vendor in China was absolutely critical for answering the many questions I had about the process. I shared many rounds of drawings and rough CAD to gain design and manufacturing feedback. This was just as much of a learning experience for the vendor as it was for me; blow-molding had only been successful at a shoe scale, not a phone scale. Challenge accepted.
TOOLING + TRIAL SAMPLES We could only make best guesses on things like wall thicknesses and parting lines for so long; eventually the only way to test and prove out my design was to just make it. I needed to see tooled parts to understand if a phone case with actual blow-molded air pockets would even be possible, so making a tool it was. High-risk, high-reward.
MANUFACTURING + ASSEMBLY Initially, I explored a few methods for how the airbags would be assembled into the case. Post-assembling the airbags by either snapping or glueing them in was the least risky approach, but resulted in a messy part that was prone to falling apart. Ultimately, it was decided to place the airbags into a tool and shoot TPU around it to create a clean, robust, single-piece part.
2
Enhanced functionality
INSPIRATION People love PopSockets already because they function as a grip and stand for their device. It was important to preserve (and enhance) these features on a case with an integrated PopSocket, but I also wanted to solve for a common problem users have with their PopSocket: snagging on pockets.
SKETCHING + IDEATION Ramping up the back surface of the case to meet the PopSocket flush does improve "pocketability," but any ramp starts to eat into the finger space under the PopSocket, making "gripability" worse. The challenge would be maintaining a ramped surface, while regaining the lost finger space.
To me, it made the most sense to re-engineer the same expanding accordion-like experience of a PopSocket onto the back of a case, so that the entire PopSocket could actually pop outwards and overcome the ramp.
PROTOTYPING Proving out a mechanism like this required prototyping in tricky materials, like rubbery soft plastic. Various prototyping techniques were used for different parts of the mechanism; both soft and hard plastic parts were 3-D printed, casted, and CNC machined.
3-D CAD MODELING + MECHANICS The pop-out mechanism experience is just as intuitive (and fun to play with) as the PopSocket itself. Simply pull twice to expand the accordion on the PopSocket, then pull a third time to expand the accordion in the case. Warning: popping this thing is highly addictive.
TOOLING + TRIAL SAMPLES Although they weren't perfect, I could not have been more stoked on the first round of trial samples. The blow-molded airbags survived the overmolding process (with some flash and short-shotting) and the pop-out mechanism worked! With some tuning to molding peramters and material durometer, this design would be a success.

Air-pockets, in your pockets.
First ever phone case with
air-pocket technology
Patent-pending
The PopSocket, upgraded. With new
pocket-friendly
pop-out mechanism
Patent-pending
PopCase AIR
for iPhone
PopSockets